Scope of Research
The research projects under HI-AM 2.0 aim to expand the applications and capabilities of Directed Energy Deposition (DED), Powder Bed Fusion (PBF), and Binder Jetting (BJT) technologies. These efforts span a broad spectrum of innovative research, including:
- Process parameter optimization for advanced alloys
- Multi-scale and multi-physics modeling of thermomechanical phenomena in AM processes
- Microstructure and digital twin modeling
- Enhancing process reliability through machine learning-based quality assurance
- Optimizing multi-laser PBF and large-envelope DED systems for scalability
Additionally, several research activities focus on life-cycle assessment (LCA) and environmental sustainability, ensuring that project outcomes align with both innovation and environmental responsibility.
Our research focuses on the following technologies:
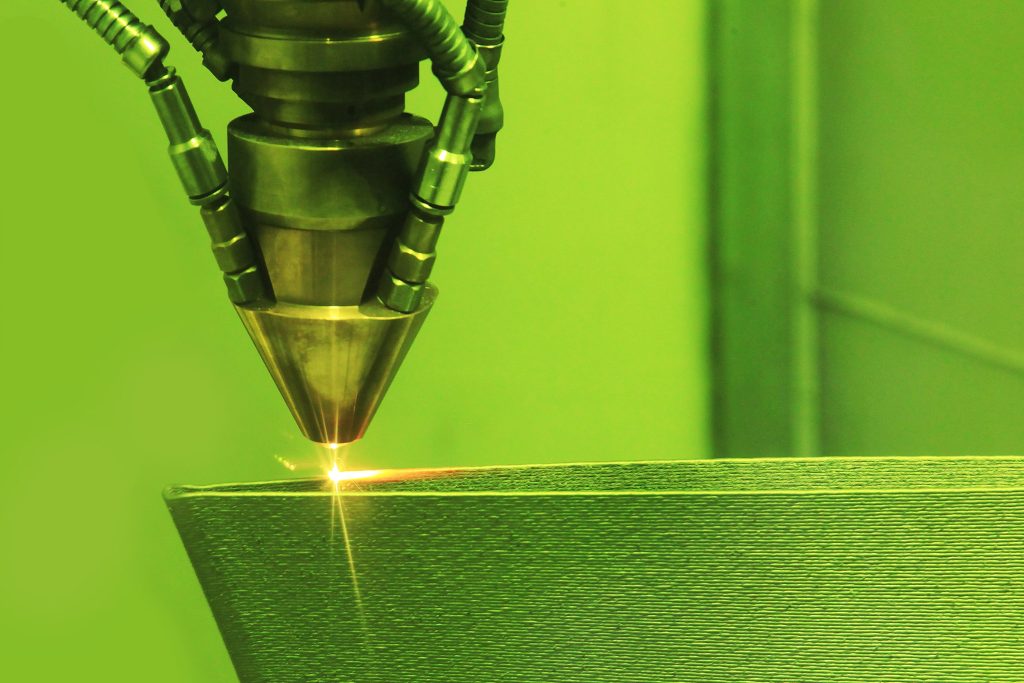
Directed Energy Deposition (DED)
- Laser DED (powder-fed and wire-fed)
- Electron beam DED
- Arc-based DED
- Cold spray DED
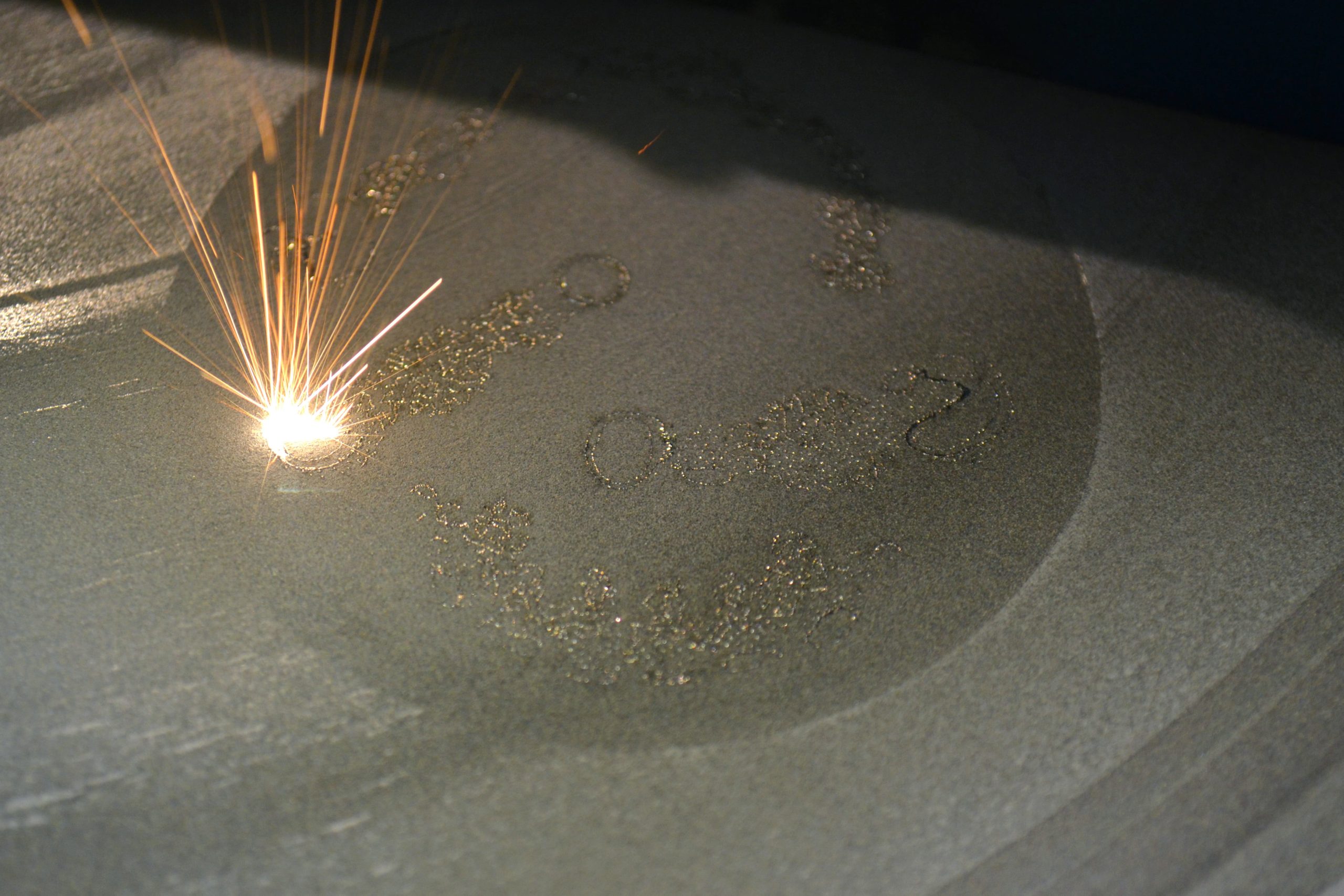
Powder Bed Fusion (PBF)
- Laser PBF (single-laser and multi-laser)
- Electron beam PBF
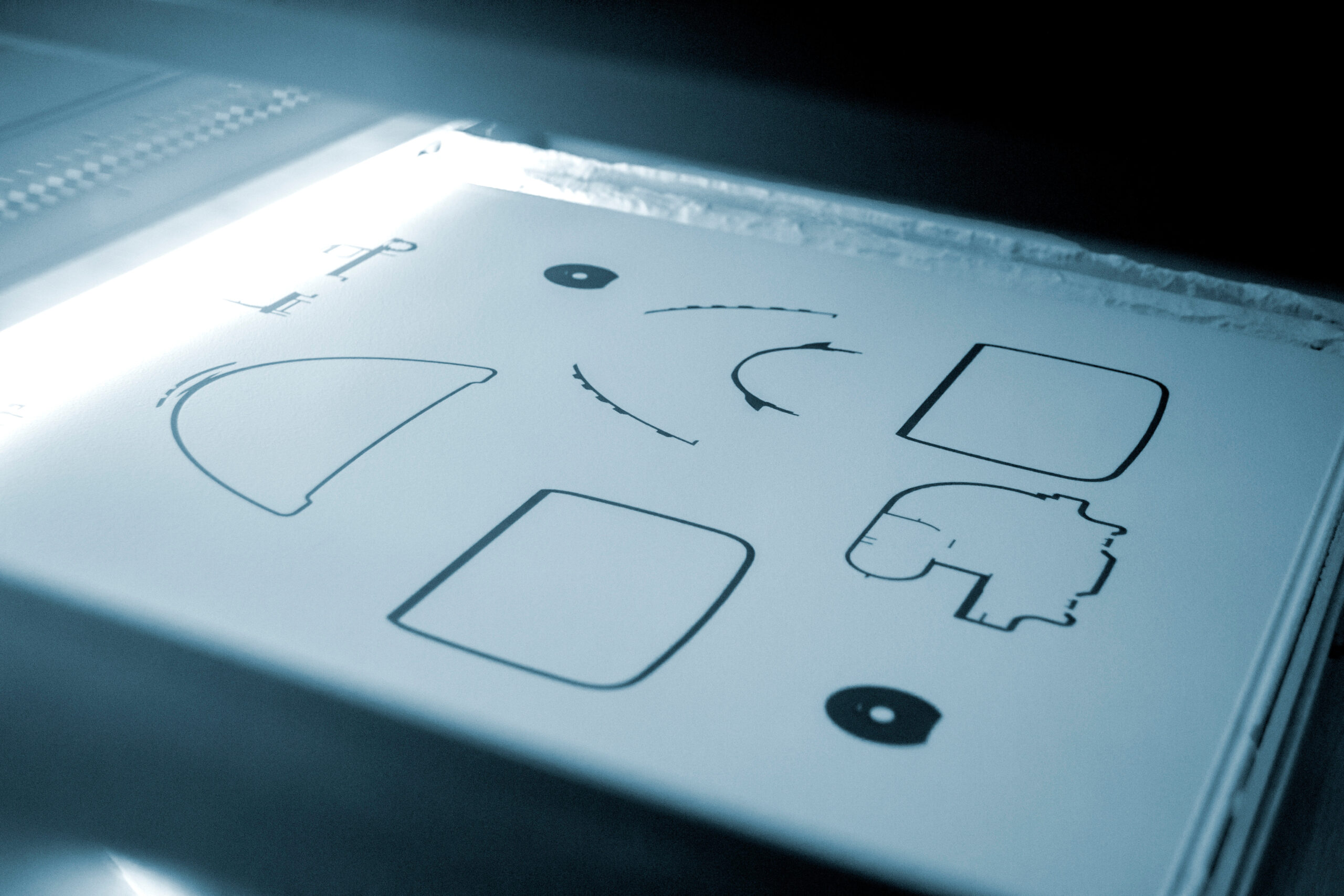
Binder Jetting (BJT)
Cross-Sector Partnerships
Our research activities are being carried out in close collaboration with leading private sector companies across key industries, including feedstock suppliers, engineering and consultancy services, aerospace, automotive, and energy. By working directly with these industry partners, we ensure that demonstrators, feasibility tests, and component designs are tailored to meet their specific needs and challenges. This partnership-driven approach enables us to align our research outcomes with real-world applications, accelerating the adoption of metal AM technologies in critical sectors.
Partners

Research Projects
The HI-AM 2.0 Project is funded by two NSERC Alliance grants, each focusing on specific AM technologies. One grant is dedicated to DED technology, while the other supports PBF and BJT technologies. Research activities for each grant are organized into two themes, each encompassing various projects, as outlined below:
Advanced multi-scale, multi-physics simulation of DED processes
Objectives:
- Develop a mesoscale computational fluid dynamics (CFD) model for L/EB-DED processes to predict solidification conditions, enabling the creation of advanced strategies for microstructure control during the repair or fabrication of high-value components
- Model the impact of heat input strategies on the microstructure and mechanical properties of high-strength steel during L-DED repair
- Develop a macro-scale finite element model for multi-axis robotic DED, incorporating hybrid plasma transferred arc and laser heat sources to enhance process accuracy and performance
Lead Principal Investigators:
Autonomous hybrid process planning for large-scale AM by robotics DED systems
Objectives:
- Develop a software toolchain for autonomous deposition and inspection of L-DED-manufactured parts, utilizing the Robot Operating System (ROS)
- Develop a software toolchain for autonomous subtractive operations using the ROS
- Integrate and validate deposition, inspection, subtractive, and obstacle avoidance nodes for streamlined system functionality
- Implement path planning for a hybrid multi-axis PTA- and L-DED system, incorporating in-process plastic deformation
Lead Principal Investigators:
AI-driven quality assurance tools for defect detection in L-DED of novel tooling
Objectives:
- Enhance the quality and robustness of L-DED processes using machine vision solutions
- Develop hybrid AM tooling to maximize the tooling longevite, incorporating the quality assurance solutions developed in previous objective
Lead Principal Investigators:
University of Waterloo, Canada
Associate Professor
Associate Director, HI-AM 2.0
Associate Director, HI-AM 2.0
Advanced impact model development for CS-DED for repair and part extension purposes
Objectives:
- Investigate the fundamentals of particle deformation and bonding at the individual particle level
- Develop machine learning algorithms for process optimization and predictive modeling to enhance CS-DED efficiency and effectiveness
Lead Principal Investigators:
New frontiers in DED of advanced materials
Objectives:
- L-DED processing of AlCoCrFeNi and FeCoNiCrMn
- Optimize L-DED process parameters for M300 deposition on L-PBF-made substrates
- PTA-DED processing of NiBSi-WC metal matrix composites
- Design functionally graded structures (FGMs) of NiBSi-WC to minimize residual stresses in the manufactured components
Lead Principal Investigators:
University of Waterloo, Canada
Associate Professor
Associate Director, HI-AM 2.0
Associate Director, HI-AM 2.0
Holistic adoption of DED for large-scale manufacturing, refurbishment, and repair
Objectives:
- Develop innovative strategies for the manufacture and repair of high-value titanium components using L/EB-DED
- Advance multi-axis robotic DED processes for producing large components for applications in the energy industry
- Investigate the impact of design and process parameters on throughput and quality for NiBSi-WC parts manufactured using PTA-DED
Lead Principal Investigators:
CS-DED repair of steel and nickel-based parts
Objectives:
- Establish the sprayability window for the powders of interest
- Develop powder conditioning and in-process strategies
Lead Principal Investigators:
Advancements in BJT of magnetic and stainless steel alloys
Objectives:
- Develop effective BJT process parameters for optimizing the fabrication of magnetic materials
- Implement BJT of SS316L and 14-4PH fine powders to achieve high dimensional fidelity and density in printed components
Lead Principal Investigators:
University of Waterloo, Canada
Associate Professor
Associate Director, HI-AM 2.0
Associate Director, HI-AM 2.0
L-PBF and BJT of high conductivity copper-based alloys
Objectives:
- Conduct BJT benchmarking for copper alloys (Cu18150, Cu14500) synthesized through gas, plasma, and microwave atomization, as well as micro-milling, alongside pure copper produced via water atomization
- L-PBF processing of copper alloys (Cu18150, Cu14500) synthesized through micro-milling
Lead Principal Investigators:
University of Waterloo, Canada
Associate Professor
Associate Director, HI-AM 2.0
Associate Director, HI-AM 2.0
Advancements in L-PBF of titanium alloys
Objectives:
- Minimize cracking in L-PBF-manufactured Ti6242 components by utilizing a quad-laser system and a high-temperature build plate
- Perform mechanical and corrosion testing on Ti6242 printed coupons
- Conduct comprehensive mechanical testing on optimally printed Ti64 samples with added contaminants
- Investigate the metallurgy of L-PBF-manufactured beta titanium alloys to enhance understanding of their properties and performance
Lead Principal Investigators:
Density, microstructure, and performance control of L-PBF/BJT-made nickel-based parts
Objectives:
- Investigate the interactive effects of sample size, service temperature, surface finish, and heat treatment on the static and cyclic properties of IN625
- BJT processing of IN625 and IN718 fine powders to achieve high dimensional fidelity and density
Lead Principal Investigators:
University of Waterloo, Canada
Associate Professor
Associate Director, HI-AM 2.0
Associate Director, HI-AM 2.0
Advancements in L-PBF adoption of low-cost high-strength aluminum alloys
Objectives:
- Determine the absorptivity scaling laws for aluminum alloys processed in L-PBF
- Optimize processes for achieving high density and mitigating cracks
Lead Principal Investigators:
University of Waterloo, Canada
Associate Professor
Associate Director, HI-AM 2.0
Associate Director, HI-AM 2.0
Accelerated multi-scale simulation of EB/L-PBF customized for digital twin modeling
Objectives:
- Develop a mesoscale CFD model for L/EB-PBF to assist in creating effective heat sources for macro-scale modeling
- Customize the accelerated L-PBF simulation package for integration into a digital twin framework
Lead Principal Investigators:
Advanced multi-scale modeling and simulation for BJT densification phenomena
Objectives:
- Calibrate the sinter curve and the 3D densification model to capture the densification and deformation behaviour in solid-phased and partial liquid-phase sintering of BJT-made components
Lead Principal Investigators:
University of Waterloo, Canada
Associate Professor
Associate Director, HI-AM 2.0
Associate Director, HI-AM 2.0
In-situ integrated optical tomography and melt pool monitoring for quality assurance
Objectives:
- Develop knowledge-based machine learning algorithms for defect detection during the L-PBF of titanium-based alloys using optical tomography (OT)
- Enable supportless printing and minimize cracks in L-PBF-manufactured Ti6242 components in a quad-laser system equipped with OT sensor
- Adopt OT and melt pool monitoring (MPM) for holistic L-PBF process optimization, leveraging integrated data augmentation and machine learning methods
Lead Principal Investigators:
Ex-situ detection of defects, entrapped powders, and security markers via linear array ultrasonic testing
Objectives:
- Tune and optimize linear array ultrasonics testing (LAUT) parameters for precise feature detection in aluminum and iron alloys
- Detect features of interest and benchmark results against CAD models and computed tomography (CT) data
Lead Principal Investigators:
University of Waterloo, Canada
Associate Professor
Associate Director, HI-AM 2.0
Associate Director, HI-AM 2.0
Multi-objective design optimization and high-fidelity simulations for the next generation of thermal and electrical power management components in electrical vehicle applications
Objectives:
- Develop or customize high-fidelity multi-scale performance simulations and field-driven designs
- Conduct experimental validations of simulation tools and the resulting part demonstrators
Lead Principal Investigators:
University of Waterloo, Canada
Associate Professor
Associate Director, HI-AM 2.0
Associate Director, HI-AM 2.0